- Home >
- Security and Safety Insights >
- Case Study: Improving Worker Safety at UC San Diego Health
Case Study: Improving Worker Safety at UC San Diego Health
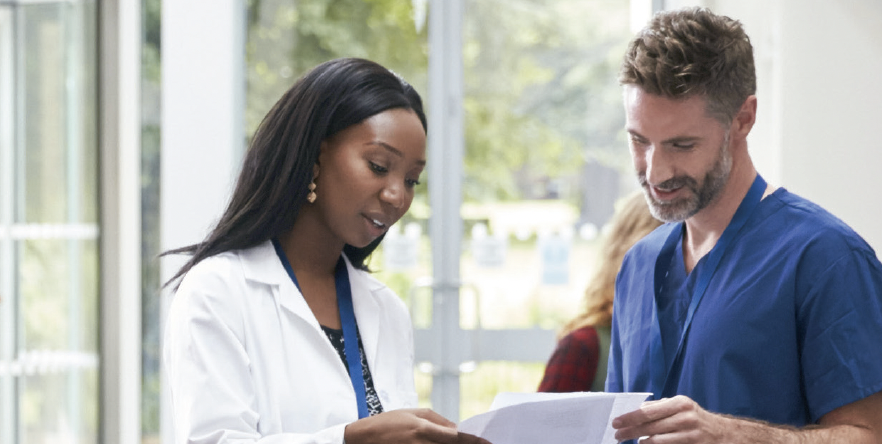
UC San Diego Health, the only academic hospital in San Diego, is one of the premier health care providers in the United States and is nationally ranked in six adult medical and surgical specialties by U.S. News & World Report. With more than 1,500 doctors and scientists who are published experts in the field, UC San Diego Health provides unparalleled patient care.
As a leading health advocate, the hospital chose to proactively evaluate the state of its lockout/tagout (LOTO) programs at its Hillcrest and La Jolla facilities to ensure the safety of its workers and prevent incidents that could jeopardize patient care. UC San Diego Health selected The Master Lock Company as its workplace safety partner because of its end-to-end safety solutions, including industry-leading expertise, innovative lockout products and consulting services.
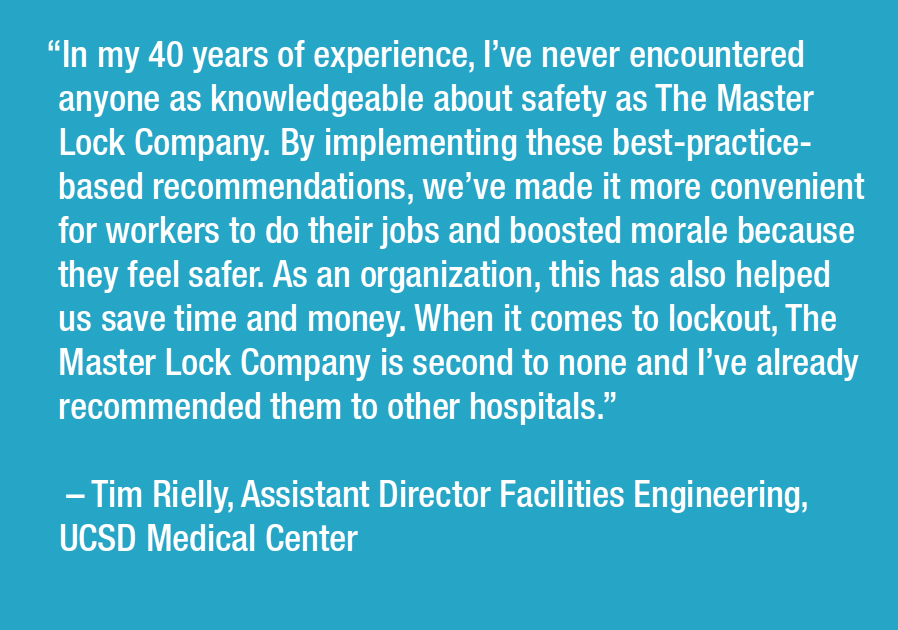
Goals & Analysis
Identifying Opportunities to Improve Worker Safety and Operational Efficiencies
UC San Diego Health’s primary goal was preventing lockout-related accidents due to the unexpected release of hazardous energy while workers maintain and operate machinery and equipment. As a secondary goal, the hospital was interested in determining whether it could improve safety-related operations and make it more convenient for workers to perform lockout procedures.
Solution
As a leader in workplace safety for nearly 30 years, The Master Lock Company worked closely with UC San Diego Health to create a safer work environment by implementing best-practice-based recommendations that achieve heightened safety, practicality and efficiency for its personnel.
Evaluating Current State of Lockout Program – To identify methods of improvement, The Master Lock Company conducted an in-depth assessment of UC San Diego Health’s lockout practices, which included:
- In-person discussions, interviews and lockout-specific assessments with participating departments
- Receiving input from safety representatives and facility lead personnel
- On-site examination and analysis of the facilities and their applications for controlling hazardous energy sources during maintenance and repair operations
After reviewing the information collected and synthesized by The Master Lock Company, UC San Diego Health concluded that the hospital system could increase the efficiency and safety of maintenance tasks performed by authorized personnel by improving access to lockout equipment.
Safety Recommendations
RAISING SAFETY AWARENESS – All workers authorized to service or repair equipment must protect themselves and their coworkers by applying lockout before every time they begin to work on machinery. This means that workers must first understand the applicable safety requirements and guidelines and then act to protect themselves and their colleagues.
To educate workers, The Master Lock Company’s Gena Hedger, a certified and experienced Lockout Practitioner and solutions provider, conducted lockout training at both UC San Diego Health facilities with all information tailored to the hospital environment. This instructor-led training covered Cal/OSHA’s Lockout standard, best practices for controlling hazardous energy, common mistakes that lead to accidents as well as the importance of personal responsibility to ensure the safety of the worker and their colleagues.
STREAMLINING SAFETY PROGRAMS – A common, universal cause of lockout-related incidents occurs when workers skip safety steps with the thought that these procedures add complexity and extra time to their work. The Master Lock Company applied “Rapid Access to Lockout Equipment” practices, which are based on lean management principles, to help UC San Diego Health improve worker access to lockout equipment.
One significant element of this was equipping authorized workers with customized Master Lock lockout safety kits. Rather than having to leave a machine’s side and retrieve the necessary safety equipment from distant storage locations, workers have all the necessary equipment on hand. This maximizes access to lockout equipment, which in turn minimizes wasted time.
Additionally, the lock out safety kits offered the following benefits:
- Simplified the performance of lockout with keyed-alike padlocks. Workers can now control all their designated padlocks with one personal key that only opens their locks.
- Prevented accidents due to miscommunication.
- The padlocks are now color coded based on department, providing staff with visual identification of which team is working on a specific piece of machinery.
- The padlocks are personalized, bearing each employee’s name laser engraved on the lock body. This drives safer behavior by instilling a sense of ownership and pride in work, in addition to increasing communication.
Conclusion & Results
After raising awareness of the importance of workplace safety, implementing best-practice-based recommendations and improving access to lockout equipment, UC San Diego Health has taken measures to improve its safety culture, increased maintenance efficiencies and ultimately created a safer work environment.
Specific results include:
- Increased efficiency – On average, UCSD Health workers now perform lockout 50% faster.
- More uniform and consistent application of lockout – All necessary equipment is quickly and easily accessed.
- Heightened participation – Through training and provision of the right equipment to do the work safely, authorized personnel realize the importance of protecting themselves and their coworkers.
Have a similar challenge? Don’t know where to start? Contact one of the Master Lock safety experts to start a conversation to see how we could help.
Visit MasterLock.com to learn more about Master Lock’s Professional Lockout Services.